Your cart is currently empty!
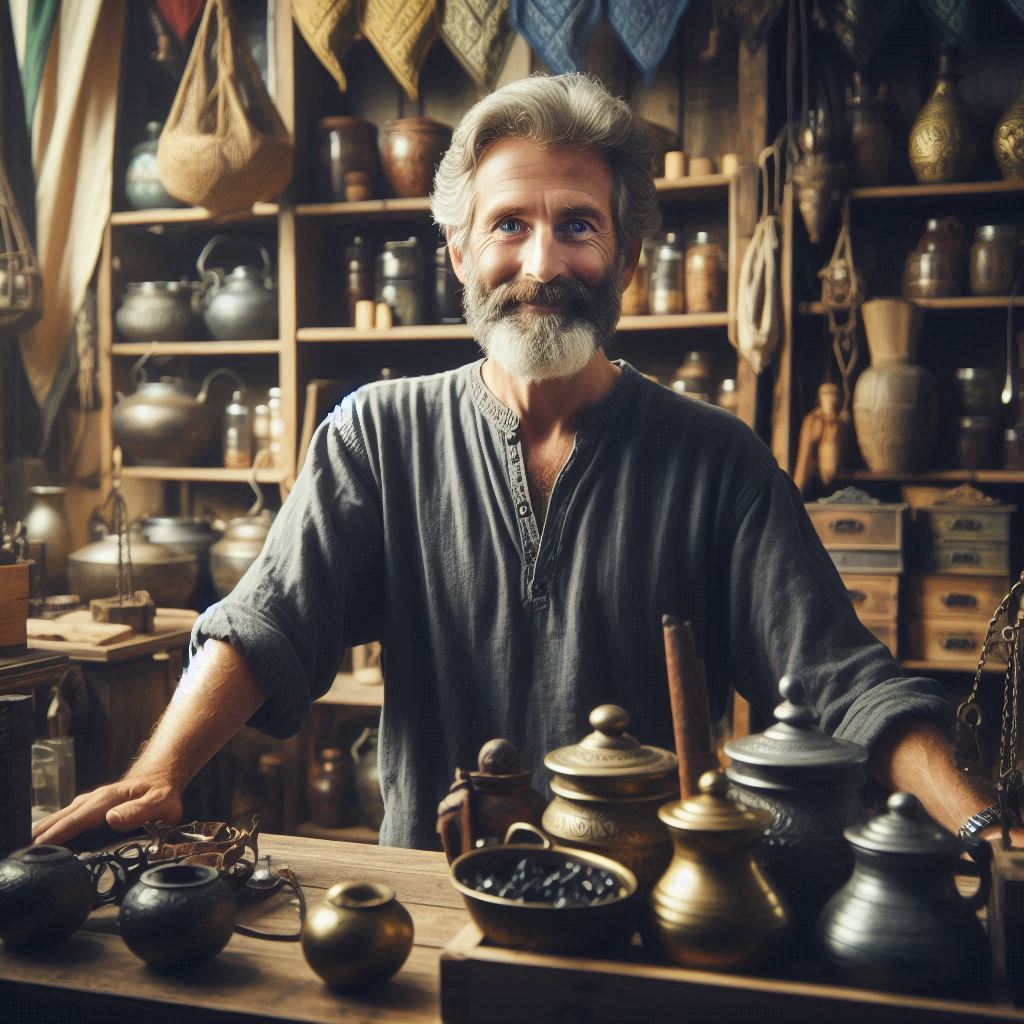
Leveling (Tramming)
Posted
by
(modified
)
One of the most important skills in 3d Printing is the ability to reliably and repeatably level (or tram) the print surface. Without a nearly perfect print surface, your print will be flawed from the beginning, and is very likely to either not adhere, adhere too strongly, or simply fail with no filament extrusion. At a very basic level, this requires your print bed to be at a precise distance away from the print head at all times, regardless of temperature, location, or print duration. Across a 200 mm surface, this tolerance should be within 0.1mm or less, if at all possible – something that is challenging and frustrating at times.

The first step I have found is making sure that your print bed itself is flat – this can be either because the print bed is particular thick (and can’t bend), or because you have replaced or supplemented it with a known flat surface (such as glass). In my case, my choice of surface is a Borosilicate glass plate (https://amzn.to/2NiV5f6) set on squares of Silicon Heat Transfer pads (https://amzn.to/2QCQBOn), on top of the default factory surface. The glass plate I know is flat by design, and the borosilicate reduces or eliminates warping and change due to temperature. The silicon pads provide both reliable heat transfer from the heated bed, allowing the glass to come up to temperature quickly, and also provide adhesion to the heated bed to keep the glass from slipping. Many people suggest the use of binder clips or other attachments to hold the glass – thus far I have found those both unnecessary (the glass never slips) and problematic since the pressure point is unreliable and shifts the glass unpredictably. A simple glass sheet on thermal pads on top of the heated bed has worked very well, and is conveniently simple to remove if cleaning is necessary.
Once you have a flat surface, you then have to make sure that the bed itself it aligned to the axis of the print head. Typically this means the X and Y axis, but that can be different with different printers. Note that this is a bit misleading – it is not that your print bed needs to be level with regards to gravity – it means that the X and Y axis need to be perpendicular to the Z axis where the print head is. Since the printer utilizes several support rails for the axis, that is the point where I work to level the carriage itself.

In my case, I first use a straight edge and a digital level, and measure the Y axis rails (the lowest ones) at both ends. You are not aiming for 0, but you are aiming for consistency. In my case, the digital level registered a -0.3 degree slope at all points in line with the rails.
You also need to measure across the rails, to get the X axis alignment. This is a common miss, and a inconsistent reading here indicates a twist to the rails. After some adjustment of the printer feet themselves, I was able to get a consistent -0.7 across the rails. This is a challenging part, since the twist may not be because of the rails themselves. In my case, the feet of the printer were not completely in line, so I have to lower one corner only to account for the twist. Again, tiny adjustments carry thru and make sizeable changes.

Once both axis are consistent in their readings, then you know that your carriage is flat and untwisted. Assuming your Z axis is perpendicular (and the tolerance there is not a tight), you should be good to go for the final leveling stage – leveling the bed to the print head itself.
This is the stage that most think of when it comes to leveling. Moving the print head around, and twisting the support knobs until it reaches the desired distance. I have seen recommendations of “use a sheet of paper” or set it to a specific distance (0.1mm is referenced). In my case, it just isn’t that clear – there always seems to be some fine tuning, and it will vary based on the nozzle you have, the filament you use, and the printer you have. A piece of paper or a 0.1mm gauge will get you in the ball park for the first pass. Note that it is recommended to do all of the fine tuning of the printer with the bed set for the typical print temperature – even borosilicate glass with expand with heat, which can throw off your measurements at this level of tolerance.
One of the big challenges here is the bed leveling system the printer has. The Maker Select Plus comes by default with a 4-point leveling system, which may make sense from the build, but does not from basic geometry. 3-points define a flat plane, 4-points define a “bent” plane. Thus my next major change was to replace the carriage with a Y-Carriage, aka a 3-point support tray (https://amzn.to/2MIrlTX). This replaces the 4-point support with only 3-points, which makes the leveling much more intuitive, but it does change the process.
- With the 3-point system, you first align the “pitch” – the axis along which two of the supports follow. Pick one of the two and that becomes your baseline. Move the print head, and then set the support screws so that the print head is at your desired tolerance of a sheet of paper or 0.1 mm. From this point forward, that support does not move – it is your baseline.
- Then move to the second “pitch” support, and set it to the proper thickness with the print head. Once that is done, your flat surface (your “plane”) is aligned to the print head along one of the axis.
- Finally, move to the “roll” axis – the third support. Move the print head again to near that point, and adjust the support to again reach your tolerance. This “rolls” the surface up or down to align with the print head. Once that is in position, and assuming you followed all the other steps to avoid twist in the support rails and you have a flat surface – you should be able to move the print head to any location, and still have the same tolerance. This confirms that you are now “leveled” to the print head.
- If you find a spot on the surface where the tolerance gap is too large, and another where it is too small – you still have a slight twist in your support rails. Go back and recheck that they are at a consistent angle. If the angles are consistent, then it is possible your print bed itself is not as flat as you might think.
Assuming you have a consistent bed, the final step is fine tuning. This is where the details of each printer model and each specific printer plays a part. At this stage, we are talking in µm, so any slight variation plays a factor.

Start by printing some alignment squares. These are nothing more than a pair of squares that print near the extremes of your print bed. You can toss together one quickly, or you are welcome to use mine from Thingiverse, https://www.thingiverse.com/thing:3105660. In your slicer, position them to print near the edges of the print bed, once set near the pitch supports, and one set on the side of the roll support. You want to print them separately (2 squares each time), to validate the specific location.
While they are printing, watch the details:
- If the surface is thin and wispy, or not printing, your bed is too close. While it is printing, adjust the print support nearest ever so slightly to lower the bed.
- If the surface is not adhering, or is pulling up, your bed is too far away. While it is printing, adjust the print support nearest ever so slightly to raise the bed. Since the filament is loose, it may dislodge the entire print, and require you to re-run the test.
- If the surface is adhering nicely, then you are aligned, and the printer is now ready to go. Once the print is done, you can remove it, and the print lines should be solid and strong. If they pull apart easily, the bed is still too far away. If they tear easily or the surface seems thin, the bed is still too close.
- Repeat the test as needed, being sure to test and adjust each support only while its respective square is printing. For the roll set, both squares should print identically, but you would only be adjusting the single support. If both squares or not the same, then reference and adjust for twist again.
Hopefully at this point, you printer is working well, and you are happy with the quality of each of the calibration squares. In theory, your printer is now leveled and ready to go. However, you need to continue observing at least the first few models, to make sure that the first layer is consistent, and that the alignment doesn’t slip. If you start getting a wispy surface, or a problem with adherence, then it is possible one of the supports have moved, and the bed is no longer in alignment. If you are like me, and you are using only silicon pads to hold the glass, this can easily happen when you remove the part from the surface, since it pulls the glass up a bit. Try to hold the glass in position if the part doesn’t release easily on its own.
Materials and Links
- Thingiverse – Calibration Squares
- Y-Carriage Upgrade – https://amzn.to/2MIrlTX
- Borosilicate Glass surface – https://amzn.to/2NiV5f6
- Silicon Thermal Pad – https://amzn.to/2QCQBOn